Leading Blow Molding Machine Manufacturer for High-Quality Production Solutions
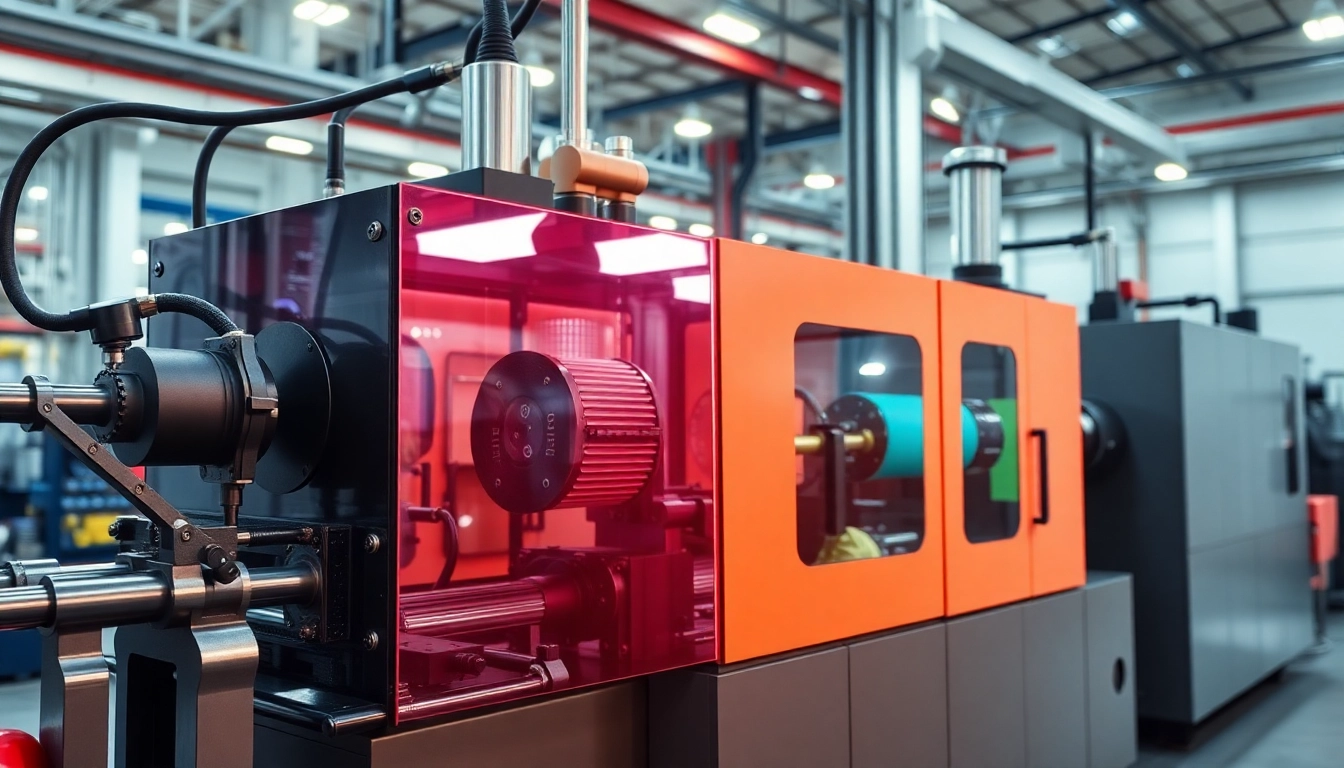
Introduction to Blow Molding Machines
Blow molding machines are vital components in the production of plastic products including bottles, containers, and tanks. These machines leverage the blow molding process to create hollow plastic objects, which are essential to various industries such as packaging, automotive, and consumer goods. As a leading Blow Molding Machine Manufacturer, understanding the intricacies of these machines can significantly impact production efficiency and product quality. This article delves into the mechanisms, applications, and innovations surrounding blow molding machines.
What is Blow Molding?
Blow molding is a manufacturing process used to produce hollow plastic parts. It involves three main steps: extrusion or injection of plastic material into a preform, inflation of the preform into a mold, and cooling to form the final shape. This technique is widely recognized for its efficiency and ability to create complex geometries, which is especially useful in high-volume production scenarios.
Types of Blow Molding Processes
There are primarily three types of blow molding processes: extrusion blow molding (EBM), injection blow molding (IBM), and stretch blow molding (SBM). Each process has its unique characteristics suitable for different applications:
- Extrusion Blow Molding (EBM): Used for producing a variety of hollow objects like bottles and containers, EBM involves melting plastic and forming a parison that is inflated into a mold.
- Injection Blow Molding (IBM): This process combines injection molding with blow molding, making it ideal for creating smaller, more complex shapes with higher precision.
- Stretch Blow Molding (SBM): Primarily used for PET bottles, SBM stretches the preform while blowing air into it, which improves the strength and clarity of the final product.
Key Applications of Blow Molding Machines
Blow molding machines find applications across various industries:
- Packaging: They are most commonly used to produce bottles, jars, and containers in the food and beverage sector.
- Automotive: Many automotive components such as fuel tanks and air ducts are produced using blow molding techniques.
- Consumer Goods: Products like toys, household containers, and personal care items benefit from blow molding due to their lightweight and durable characteristics.
- Medical: Specialized blow molding processes help manufacture medical components that require stringent regulation compliance.
Choosing the Right Blow Molding Machine Manufacturer
Selecting an appropriate blow molding machine manufacturer can be a challenging task, particularly given the variety of options and technologies available. It’s crucial to focus on several key aspects to ensure you choose a manufacturer that meets your specific needs.
Factors to Consider: Quality and Reliability
The quality and reliability of blow molding machines are paramount. Look for manufacturers who adhere to international quality standards and have a reputation for producing durable machines. Customers should seek out product specifications, durability tests, and certifications that affirm the machine’s reliability. Reading testimonials and reviews from past clients can provide invaluable insights into the quality of their machines.
Evaluating Manufacturer Experience and Innovation
Experience in the industry often translates into a deeper understanding of market demands and technological advancements. A manufacturer with a track record of innovation is likely to offer machines that incorporate the latest technology, leading to enhanced efficiency and lower operational costs. It’s beneficial to research a manufacturer’s history, the technologies they employ, and any awards or recognitions they have received.
Customer Support and After-Sales Services
Customer support is critical in the manufacturing process. The right manufacturer will not only provide machines but also ensure ongoing support and maintenance after the sale. Inquire about training, spare parts availability, and technical support. A responsive and knowledgeable support team can significantly reduce downtime and improve production efficiency.
Benefits of Custom Blow Molding Solutions
One of the significant advantages of working with an experienced blow molding machine manufacturer is the ability to receive customized solutions tailored to specific production needs.
Customization for Specific Industry Needs
Every industry has unique requirements influenced by the products they manufacture. Custom blow molding solutions allow companies to specify machine configurations and features that best match their production goals. This flexibility can include adjustments in cavity design, mold materials, and machine specifications. Ultimately, customization can lead to enhanced product quality and increased market competitiveness.
Benefits of Automation and Efficiency
Modern blow molding machines often come equipped with automated features to streamline production processes. Automation reduces labor costs, minimizes human error, and increases output consistency. Integration with data analytics and Industry 4.0 technologies allows manufacturers to monitor machine performance in real-time, thus enhancing operational efficiency. Automated blow molding solutions can also improve safety in the workplace by reducing direct human intervention in potentially hazardous areas.
Cost-Effectiveness of Tailored Solutions
While the initial investment in tailored solutions may be higher, the long-term benefits often justify the cost. Customized blow molding machines can enhance output quality, reduce material waste, and improve energy efficiency. Consequently, businesses will likely save money on raw materials and operation costs. Furthermore, a well-optimized machine can lead to faster production cycles, maximizing profits over time.
Technological Advancements in Blow Molding Machines
In recent years, the blow molding industry has seen rapid advancements in technology, particularly influenced by the growing trend of Industry 4.0. These changes are shaping how machines are designed, operated, and optimized.
Impact of Industry 4.0 on Manufacturing
Industry 4.0 introduces smart technologies to manufacturing processes. For the blow molding machine sector, this means integrating IoT (Internet of Things) devices for remote monitoring and control, predictive maintenance using AI algorithms, and enhanced data analysis capabilities. These innovations significantly improve machine performance and reliability while enabling manufacturers to adapt to changing market demands quickly.
Innovative Materials and Processes
The materials used in blow molding have seen innovation in recent years. Advanced polymers and biodegradable options are increasingly popular as industries focus on sustainability and eco-friendliness. Utilizing innovative materials not only contributes to environmentally conscious production practices but also helps companies differentiate their products in competitive markets. Additionally, new blow molding processes are being developed to cater to these materials, ensuring optimal forming and finishing.
Future Trends in Blow Molding Technology
As technology continues to evolve, several trends are emerging that will shape the future of blow molding machines:
- Increased Automation: The trend towards fully automated systems will continue, with robotics and smart sensors further enhancing productivity.
- Sustainability Focus: As environmental regulations tighten, manufacturers will increasingly require machines that can handle recycled materials and minimize waste.
- On-Demand Production: The rise of customized products will drive demand for blow molding solutions that can adapt quickly to specific orders without compromising efficiency.
Case Studies: Success Stories of Blow Molding Applications
Examining real-world applications of blow molding technology can provide valuable insights into its effectiveness and versatility. Below are several industry examples highlighting successful implementations of blow molding technology.
Industry Examples of Effective Blow Molding
In the bottling industry, a leading beverage manufacturer adopted a custom EBM solution that allows for rapid changeovers between products. This flexibility led to a significant increase in production efficiency, allowing the company to respond quickly to seasonal demands without incurring substantial downtime. Similarly, an automotive component supplier improved operational capacity by integrating stretch blow molding techniques, resulting in lightweight yet sturdy parts that met the industry’s strict safety standards.
Analyzing Customer Satisfaction and Feedback
Customer satisfaction plays a crucial role in assessing the efficacy of blow molding solutions. Feedback from companies utilizing blow molding technology indicates improvements in product quality and efficiency. For instance, a recent survey revealed that over 80% of users reported a reduction in defective products after switching to automated blow molding machines, which offered more consistent quality control through advanced monitoring systems.
Visualizing Production Efficiency and Output
Data visualization tools have become increasingly important in accessing production efficiency metrics. Many manufacturers use software that tracks key performance indicators (KPIs) such as cycle time, material efficiency, and overall equipment effectiveness (OEE). This data enables manufacturers to make informed adjustments to their processes, thus optimizing output and minimizing waste.
Leave a Comment