Ensuring Safety: The Essential Role of Hydrogen Chloride Monitors in Industrial Environments
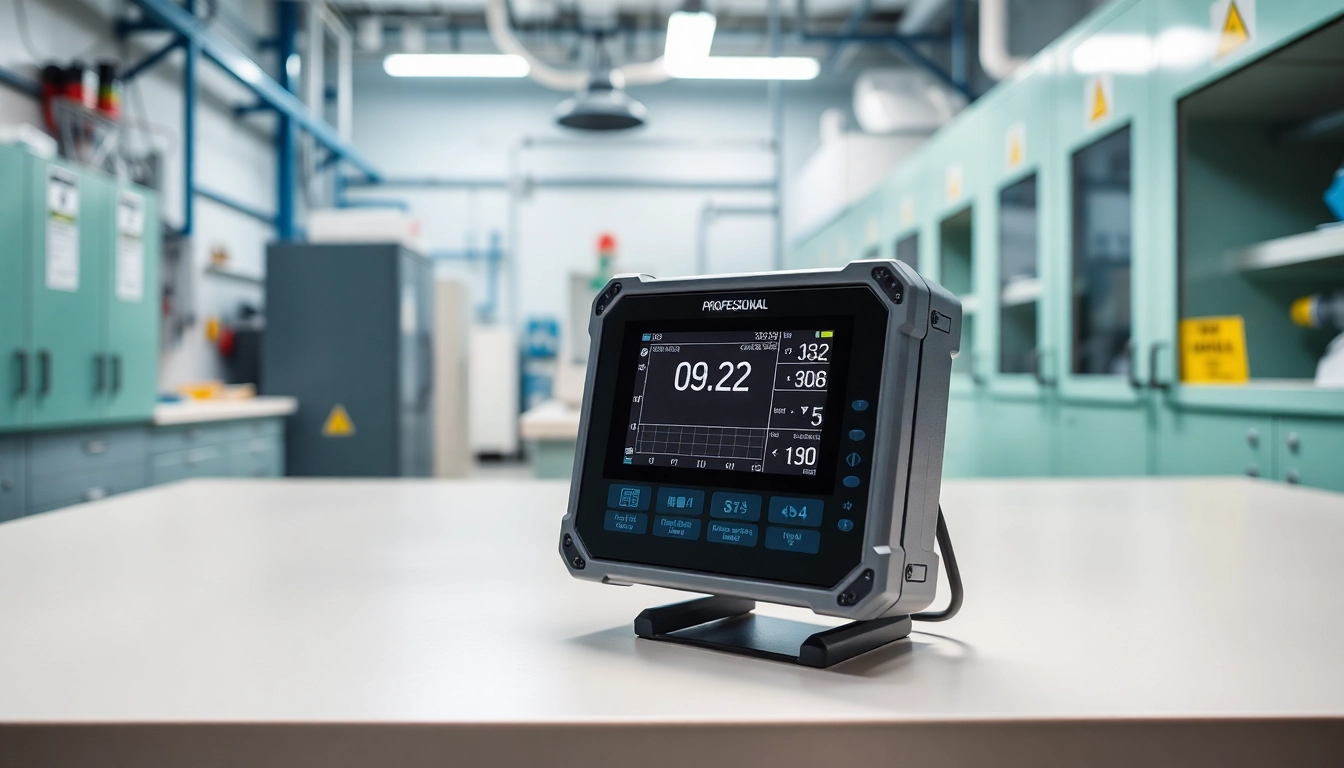
Understanding Hydrogen Chloride and Its Risks
What is Hydrogen Chloride?
Hydrogen chloride (HCl) is a colorless gas at room temperature and pressure, characterized by a pungent, irritating odor. When dissolved in water, it forms hydrochloric acid, a highly corrosive solution commonly utilized in various industrial processes, including metal processing, chemical synthesis, and the production of chlorides. Due to its inherent properties, hydrogen chloride is classified as a hazardous material, requiring stringent monitoring and management to ensure safety in environments where it is present.
Health Hazards Associated with Hydrogen Chloride Exposure
Exposure to hydrogen chloride can pose significant health risks, particularly in concentrations exceeding established safety levels. Inhalation of HCl vapors can lead to serious respiratory problems, including burns to the mucous membranes of the nose, throat, and lungs. Symptoms may range from coughing and choking to more severe outcomes like chemical pneumonitis. Prolonged exposure can also lead to chronic injury to the respiratory tract and other serious health complications. Furthermore, skin contact with hydrogen chloride can result in corrosive injuries, indicating the critical need for effective monitoring in workplaces handling this chemical.
Regulatory Standards for Hydrogen Chloride Monitoring
Due to the potential hazards associated with hydrogen chloride, numerous regulatory agencies have established guidelines for its monitoring. The Occupational Safety and Health Administration (OSHA) outlines permissible exposure limits (PEL) for HCl in workplace environments, while the American Conference of Governmental and Industrial Hygienists (ACGIH) has set threshold limit values (TLV). Compliance with these regulations not only protects workers but also minimizes the liability for organizations by ensuring safe operational practices. Proper monitoring systems, therefore, play a pivotal role in adhering to these standards and ensuring the safety of personnel.
The Importance of Hydrogen Chloride Monitors
Why Accurate Monitoring is Essential
The significance of reliable monitoring cannot be overstated when it comes to hydrogen chloride. An accurate Hydrogen Chloride monitor is crucial for detecting airborne concentrations of the gas, thereby mitigating health risks before they escalate into emergencies. Early detection allows prompt response to leaks or spikes in concentration, ultimately safeguarding workers’ health and allowing operations to continue without distress. Moreover, accurate monitoring contributes to environmental protection by ensuring that emissions do not exceed regulated limits.
Choosing the Right Monitor for Your Environment
Selecting the appropriate monitor involves evaluating several factors, including the specific application, the environment’s conditions, and the required sensitivity range. Different industries have varied requirements; for instance, a refining operation may need a high-sensitivity monitor compared to a smaller laboratory. Additionally, it is crucial to consider factors like temperature, humidity, and the presence of other chemicals that might interfere with sensor operation. Engaging with vendors or safety consultants can provide valuable insights into making the best choice tailored to unique operational needs.
Common Applications in Various Industries
Hydrogen chloride monitoring finds application across several sectors, including chemical manufacturing, pharmaceuticals, water treatment, and food processing. In chemical manufacturing, monitors are essential for detecting leaks and ensuring that levels remain within safe thresholds to protect workers and the environment. In the pharmaceutical industry, strict adherence to safety regulations necessitates consistent monitoring for compliance purposes. Water treatment facilities employ hydrogen chloride in pH control; thus, monitoring is vital to maintain safe operational parameters while ensuring the quality of drinking water supplied to communities. Understanding the specific needs of each industry is fundamental to employing these monitors effectively and affordably.
Technology Behind Hydrogen Chloride Monitors
Types of Hydrogen Chloride Detection Technologies
Various technologies exist for the detection of hydrogen chloride, each with its advantages and limitations. The most common types include electrochemical sensors, infrared sensors, and colorimetric tubes. Electrochemical sensors are widely used for their sensitivity and specificity but may require frequent calibration and maintenance. Infrared sensors are effective for long-range detection and are less affected by environmental conditions but can be more expensive. Colorimetric detection provides a visual indicator but is often less precise, making it suitable for initial screenings rather than continuous monitoring. Understanding these technologies helps industries to select the most effective approach for their safety needs.
Calibration and Accuracy of Monitors
Calibration is critical for the accuracy of hydrogen chloride monitors. It involves adjusting the device to align with a known standard or reference concentration. Regular calibration ensures that monitors provide reliable readings, which is pivotal for health and safety decisions. Different manufacturers may have varied calibration protocols, but best practices generally recommend periodic checks—monthly or quarterly depending on the monitor type and environmental conditions. Accuracy can also be affected by factors such as sensor drift and environmental interference, necessitating comprehensive knowledge of operational standards to maintain performance.
Maintenance Best Practices to Ensure Reliability
Routine maintenance of hydrogen chloride monitors is essential to ensure longevity and reliability. Key maintenance practices include regular cleaning of sensors, battery checks if applicable, and ensuring that all components are functioning correctly. Additionally, keeping a log of maintenance actions can help identify trends or issues that may arise over time. Enlisting trained personnel for the maintenance process can significantly enhance instrument reliability and safety during regular operations.
Implementing a Hydrogen Chloride Monitoring System
Steps to Integrate Monitors into Your Safety Protocols
Implementing a hydrogen chloride monitoring system involves a series of key steps to ensure effective integration into existing safety protocols. Initially, identifying locations where exposure is likely to occur is critical. Next, selecting and deploying appropriate monitoring devices based on risk assessments should follow. It’s wise to ensure that all personnel are informed and trained in the use of these devices. Finally, establishing a regular review process of the monitoring system and safety protocols ensures that they remain relevant and effective against evolving risks.
Training Staff on Proper Usage
Training staff on the proper use of hydrogen chloride monitors is paramount to ensuring workplace safety. This includes educating them on how to operate the devices, interpret readings, and respond appropriately to alerts. Regular training sessions not only enhance knowledge retention but also promote a culture of safety within the workplace. Additionally, utilizing simulations of potential leak scenarios can prepare employees for real-world emergencies and bolster their confidence in using the monitoring equipment effectively.
Establishing Emergency Response Procedures
Establishing clear emergency response procedures is essential for managing potential hydrogen chloride exposure incidents. All employees should be aware of evacuation routes, first-aid measures, and who to contact in the event of a leak. Regular drills and updates to these procedures are necessary, as they keep preparedness at the forefront of workplace culture. Incorporating feedback from workers about potential improvements can lead to the development of a more resilient emergency response plan, ultimately minimizing health risks associated with hydrogen chloride hazards.
Evaluating the Performance of Your Monitoring System
Key Metrics to Monitor Effectiveness
Evaluating the performance of your hydrogen chloride monitoring system involves tracking key metrics over time. Critical metrics include the frequency of alerts triggered, response times to alerts, and the correlation of detected concentrations with compliance requirements. Monitoring these factors helps organizations assess the system’s effectiveness and identify areas for improvement. Incorporating technology that allows for real-time data analysis can streamline this process and provide actionable insights swiftly.
Case Studies on Successful Implementations
Numerous case studies demonstrate the successful implementation of hydrogen chloride monitors across various industries. One notable example is a large chemical manufacturing plant where the installation of advanced detection systems led to the reduction of uncontrolled release incidents by over 60%. Another case involved a water treatment facility that integrated automated monitoring systems, improving compliance with regulatory standards and enhancing the overall quality of service provided to local communities. These cases illustrate the tangible benefits of proper monitoring and highlight best practices that can be adapted by other organizations.
Regular Review and Improvement Strategies
Regular reviews of monitoring protocols, technology functionality, and associated training programs are essential in a sustained effort to improve hydrogen chloride safety measures. Organizations should establish timelines for evaluating their safety protocols and performing upgrades when necessary to meet changing regulations or to incorporate emerging technologies. Gathering input from employees and stakeholders can provide valuable insights into potential weaknesses in existing systems, ensuring continuous improvement and evolution of safety practices.
Leave a Comment