Elevate Your Production with Leading Blow Molding Machine Manufacturer Solutions
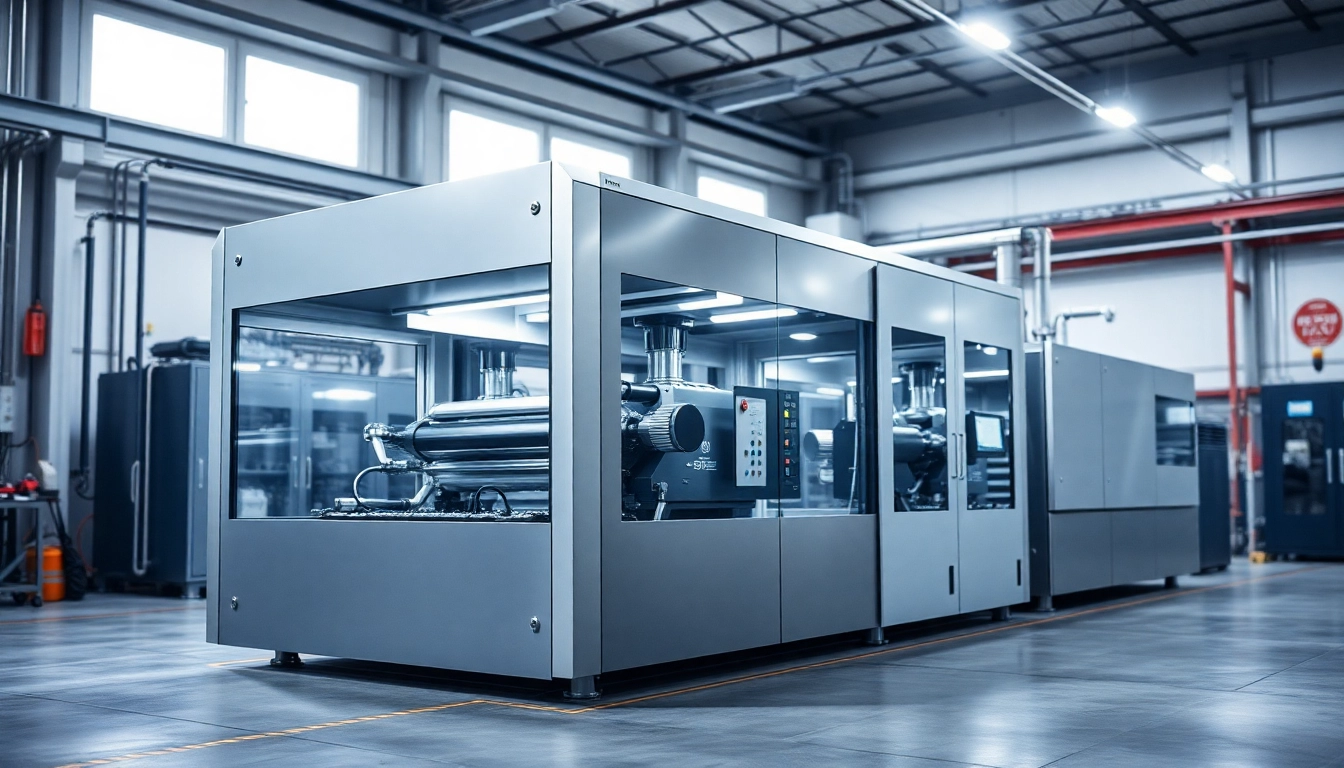
Understanding Blow Molding Technology
In the realm of plastic manufacturing, Blow Molding Machine Manufacturers play a critical role in producing hollow plastic parts efficiently and effectively. Blow molding technology is a sophisticated process used to create a myriad of products ranging from bottles to complex containers. Understanding its fundamentals, types, and applications is pivotal for businesses eager to leverage this manufacturing prowess.
Basics of Blow Molding
Blow molding is a manufacturing process that transforms thermoplastic materials into hollow shapes. The core of the process involves three main steps:
- Extrusion or Injection: In extrusion blow molding (EBM), molten plastic is extruded into a parison, while in injection blow molding (IBM), the plastic is injected into a mold.
- Blowing: Once the parison is formed, it is inflated by blowing air into it while within the mold. This inflation shapes the hot plastic into the desired form.
- Cooling and Ejection: After the plastic has cooled and solidified, the product is ejected from the mold.
Types of Blow Molding Processes
Understanding the different processes in blow molding is essential for selecting the right technology for your product line. The two primary types of blow molding processes include:
- Extrusion Blow Molding (EBM): This method is ideal for producing large containers like jugs or drums. The efficiency of the process is enhanced by producing multiple items simultaneously in a single cycle.
- Injection Blow Molding (IBM): Popular for smaller, more intricate items such as cosmetics containers. The IBM process allows for tighter tolerances and improved surface finish, making it widely chosen for high-value products.
Applications in Various Industries
The breadth of applications for blow molding is vast, making it a versatile choice across numerous industries:
- Food and Beverage: Manufacturing bottles and containers that require stringent safety standards.
- Consumer Goods: Production of cosmetics and cleaning product bottles, where aesthetics play a vital role.
- Automotive: Creating hollow parts, such as fuel tanks and air ducts.
- Medical: Producing containers for pharmaceuticals that maintain the integrity of sensitive compounds.
Choosing the Right Blow Molding Machine
When considering a blow molding machine, it’s crucial to evaluate certain factors that align with your operational needs and product specifications. The right choice can enhance production efficiency and product quality.
Evaluating Machine Specifications
Every blow molding machine comes with its own set of specifications that dictate its capabilities. Key specifications to consider include:
- Output Capacity: The number of units produced per hour impacts the overall productivity and should align with market demand.
- Mold Type: Selecting a machine that accommodates interchangeable molds can increase versatility.
- Machine Size and Footprint: Ensure the machine fits within your operational space without compromising workflow efficiency.
Key Features to Look For
Beyond specifications, several key features can enhance the usability and performance of blow molding machines:
- Energy Efficiency: Machines employing energy-saving technologies can reduce operational costs significantly.
- Automation Capabilities: Automated processes can help minimize manual labor and enhance consistent product quality.
- Data Collection: Machines equipped with sensors can provide real-time data on production metrics, allowing for informed decision-making.
Comparing Different Manufacturers
It’s crucial to investigate various blow molding machine manufacturers. Renowned names in the market, such as Uniloy, Wilmington Machinery, and Jomar Corporation, are known for their advanced technologies and reliable solutions. Each manufacturer may offer distinct advantages:
- Uniloy: Offers a range of blow molding technologies and is recognized for its global reach and service.
- Wilmington Machinery: Specializes in high-speed rotary machines, perfect for medium to large-scale production.
- Jomar Corporation: Has a significant market share in injection blow molding, catering to niche requirements.
Industry Innovations and Trends
As the blow molding industry evolves, numerous innovations are reshaping how products are manufactured and consumed. Staying informed about these advancements can guide strategic business decisions.
Latest Technological Advancements
Blow molding technology is witnessing cutting-edge advancements, including:
- 3D Printing Integration: Some manufacturers are now using 3D printing for prototyping molds, significantly reducing the time from design to production.
- Advanced Materials: The introduction of bio-resins and recycled materials is gaining traction, catering to environmentally conscious consumers.
- Robotics: Automation and robotics are streamlining operations, increasing precision, and reducing labor costs.
Energy Efficiency in Blow Molding
Energy efficiency is becoming paramount in modern manufacturing. Blow molding machines equipped with energy-efficient motors and regenerative braking systems can drastically reduce electricity consumption and operational costs. Manufacturers are actively seeking ways to promote sustainability without compromising output.
Smart Manufacturing Solutions
The rise of Industry 4.0 is prompting blow molding manufacturers to adopt smart manufacturing solutions. The integration of IoT technologies allows for real-time monitoring, predictive maintenance, and data-driven decision-making, enhancing both production capabilities and operational efficiency.
Service and Support for Blow Molding Equipment
Investing in a blow molding machine is just the beginning. Ensuring ongoing support and maintenance is critical to sustaining productivity and minimizing downtime.
Maintenance Best Practices
Maintaining blow molding machines requires dedication and experience. Some best practices include:
- Regular Inspections: Frequent checks ensure that the machine’s components are functioning properly.
- Cleanliness: Keeping the machine clean can prevent material contamination and ensure quality output.
- Training Personnel: Ensuring operators are well-trained in best practices will minimize operational errors and extend machinery lifespan.
Finding Reliable Parts Suppliers
A reliable parts supplier is essential for minimizing downtime. Companies should seek suppliers that offer genuine parts with warranties, ensuring compatibility with specific machine models and maintaining overall performance standards.
Upgrades and Customization Options
As production needs change, the option for upgrades and customizations in blow molding machines can be invaluable. Manufacturers are increasingly offering modular upgrades that can enhance existing systems without the need for entire new machine purchases, fostering long-term relationships between machine manufacturers and businesses.
Case Studies of Successful Implementation
Examining real-world applications of blow molding technology can provide insights into its effectiveness and showcase how different manufacturers thrive.
Impact of Advanced Blow Molding Machines
Case studies have revealed that companies investing in advanced blow molding technology see significant improvements in productivity and quality. For instance, a beverage company reported a 30% increase in output after upgrading to a high-speed EBM system, demonstrating the tangible benefits of modern machinery.
Customer Success Stories
Numerous companies have shared their success stories by adopting blow molding techniques. A cosmetics manufacturer that transitioned to an IBM system narrated how it not only improved product aesthetics but also reduced waste by 50% due to increased precision in molding.
Real-World Performance Metrics
In another instance, a company focused on automotive parts reduced its production cycle by 25% through investment in automated blow molding solutions, highlighting the efficiency and reliability of modern systems.
Leave a Comment