Precision Die Cutting: Elevate Your Custom Manufacturing Solutions
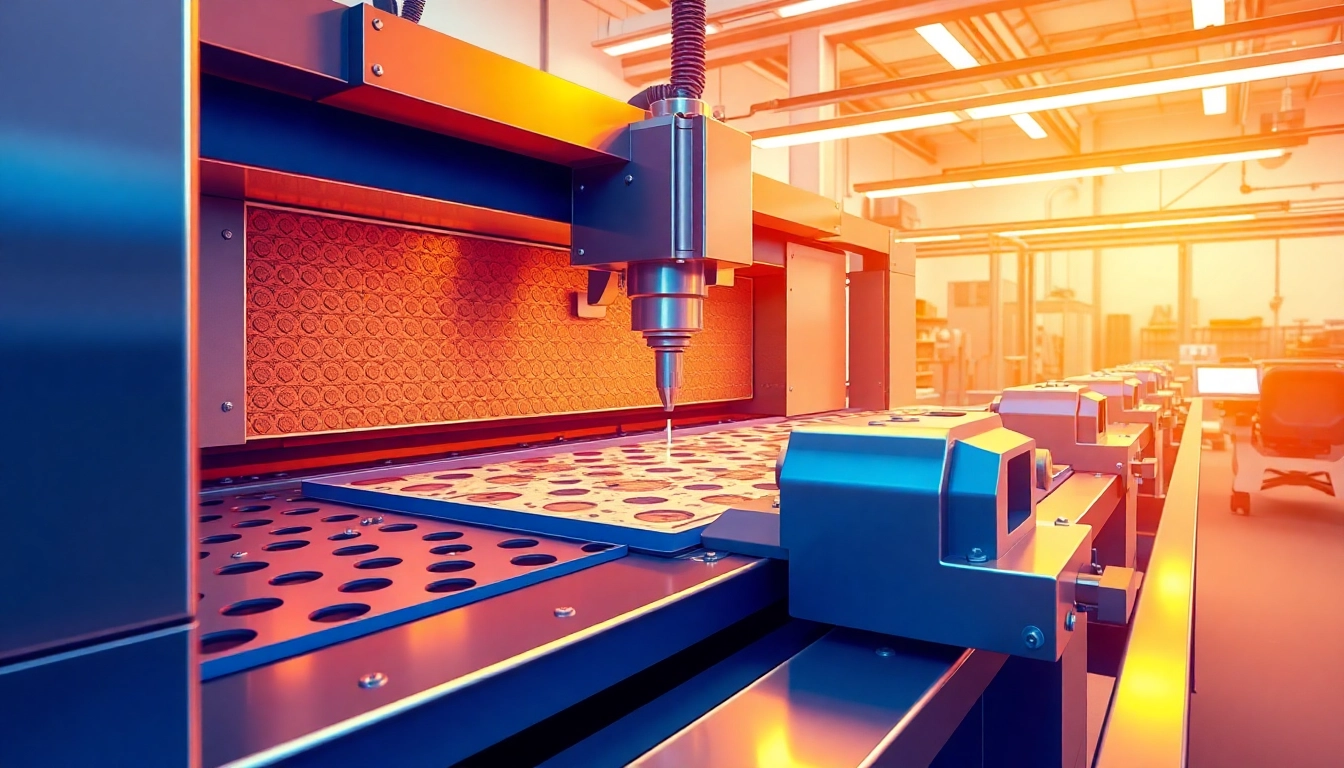
Understanding Precision Die Cutting
In the realm of manufacturing and custom production, precision die cutting serves as a cornerstone technique that allows for the creation of intricate shapes and components from various materials. This method is not only about cutting; it encompasses a meticulous process that demands accuracy, consistency, and expertise. The versatility of precision die cutting makes it invaluable across a myriad of industries—from automotive to medical devices, and packaging to electronics. The ability to produce high-quality, repeatable parts is integral to maintaining efficiency and cost-effectiveness in modern manufacturing.
To delve deeper into this topic, we focus on precision die cutting, exploring its applications, benefits, and the techniques employed to achieve superior results.
What is Precision Die Cutting?
Precision die cutting is a manufacturing process that involves cutting material using a specialized die that shapes the material to the exact specifications required for the final product. The term “precision” signifies the process’s capability to deliver parts with extremely tight tolerances, often within a few thousandths of an inch. This level of precision is crucial in industries where the fit and functionality of parts are paramount.
Materials commonly processed through precision die cutting include paper, plastic, foam, rubber, and metals. The process is utilized to produce a wide array of components such as gaskets, seals, labels, and custom packaging elements. By utilizing advanced technologies, manufacturers can ensure that the cut parts not only meet dimensional specifications but also exhibit uniform thickness and quality across large volumes.
Key Applications of Precision Die Cutting
Precision die cutting is integral in various sectors, enabling manufacturers to produce distinct parts that serve specific functions. Below are key applications where this technique excels:
- Automotive Industry: In vehicle manufacturing, precision die cutting is employed to create gaskets, seals, and insulation components that require exact specifications to ensure functionality and safety.
- Packaging: Businesses leverage precision die cutting to craft custom packaging from various materials, including cardboard and plastic, which must meet stringent design and structural requirements.
- Electronics: The electronics sector benefits from precision die cutting for components such as insulators, spacers, and connectors that necessitate precise dimensional accuracy.
- Medical Devices: Medical device manufacturers utilize precision die cutting for items like surgical pads, filters, and custom-shaped components that require adherence to strict regulatory standards.
Benefits of Precision Die Cutting in Manufacturing
The advantages of incorporating precision die cutting into manufacturing processes are manifold:
- High Quality and Consistency: One of the primary benefits is the ability to produce consistently high-quality parts. By utilizing precision machinery and technology, manufacturers can achieve repeatability in each product batch.
- Efficiency: Precision die cutting is highly efficient, allowing for rapid production times and minimal waste. The process can quickly produce large quantities of components, reducing lead times significantly.
- Cost-Effectiveness: By minimizing material waste and optimizing production processes, precision die cutting can be a cost-efficient solution for manufacturers, especially over large production runs.
- Design Versatility: It allows for complex designs that would be difficult or impossible to achieve through other manufacturing methods, such as traditional cutting or molding.
Types of Precision Die Cutting Techniques
Several die cutting techniques are available, each tailored to specific applications and material types. Choosing the right method is essential for achieving desired results.
Flatbed Die Cutting Explained
Flatbed die cutting utilizes a flat surface where a hydraulic press applies force to a die that cuts the material. This method is ideal for larger sheets and offers the ability to cut a wide range of materials. One of the primary advantages is its ability to accommodate thicker materials, making it suitable for items such as gaskets and heavy-duty packaging.
However, it can be slower than other methods, particularly for high-volume productions, as the setup process can be time-consuming. Yet, it provides an excellent approach for low to moderate volume runs where precision is required.
Rotary Die Cutting Overview
Rotary die cutting employs a cylindrical die that cuts as it rotates, allowing for continuous production. This technique is particularly beneficial for high-volume runs of thinner materials. The rotary process is characterized by its speed and efficiency, making it ideal for applications in packaging, labels, and flexible components.
Due to its dynamic nature, rotary die-cutting can also incorporate printing and other processes into the same workflow, further increasing efficiency.
Laser Die Cutting Technology
Laser die cutting uses focused laser beams to cut and engrave materials with precision. This method excels in delivering intricate designs and is often used for materials such as paper, fabric, and soft metals. The precision of laser cutting ensures high accuracy, even with complex shapes.
One significant benefit is the lack of tooling required, which reduces setup times and costs, especially for prototype development or low-volume runs. However, laser cutting may not be ideal for thicker materials, where traditional die cutting techniques might provide better results.
Choosing the Right Precision Die Cutting Provider
Selecting an appropriate vendor for precision die cutting is crucial for the success of your project. Here are key factors to consider:
Evaluating Vendor Expertise and Experience
When choosing a die cutting provider, it is essential to evaluate their expertise and industry experience. Look for companies that have a proven track record in your specific industry and can provide examples of similar projects. A knowledgeable vendor will understand the nuances of your requirements and help optimize the design and material selection.
Cost Considerations for Precision Die Cutting Services
While costs can vary widely depending on the complexity of the project, materials used, and volume of production, it is critical to request detailed quotes that outline all potential expenses. It’s worth considering the long-term costs rather than just initial estimates, as higher upfront costs could lead to better results and lower overall expenses due to efficiency and reduced waste.
Critical Quality Assurance Practices
Every reputable precision die cutting provider should have stringent quality assurance practices in place. This may include inspection protocols to ensure that every part meets specified tolerances and characteristics. Confirm that the provider utilizes modern technology, such as computerized measurements or automated inspection processes, which can help reduce error rates and enhance quality control.
Challenges Faced in Precision Die Cutting
Despite its advantages, precision die cutting is not without challenges. Understanding these challenges helps in proactively addressing them.
Common Materials Used in Precision Die Cutting
A range of materials can be used in precision die cutting, each presenting unique challenges:
- Papers and Cardboards: While easy to cut, these materials can be prone to tearing or inconsistencies if not handled properly.
- Films and Plastics: These materials can be challenging due to their tendency to warp or slip during cutting.
- Foams: Foam materials can compress under pressure, making it difficult to achieve the desired dimensions.
- Metals: Precision cutting of metals requires robust machinery and skilled operators, given their rigidity and need for high tolerances.
Tolerance Standards for Precision Die Cutting Parts
The tolerances for die-cut parts can significantly affect their functionality and performance. Typical tolerances for steel rule dies range from +/- 0.005 inches, while tighter tolerances may be required for critical applications, particularly in the aerospace and medical industries. It is essential to communicate specific tolerance requirements to the die cutting vendor to ensure appropriate manufacturing capabilities are in place.
Addressing Common Mistakes in Die Cutting Design
Mistakes in design can lead to costly production errors. Common issues include ignoring material properties, not accounting for machining limits, and failing to collaborate closely with manufacturers during the design phase. Engaging in early discussions with your die-cutting provider can help mitigate these risks and lead to a more streamlined and successful production process.
Future Trends in Precision Die Cutting
The field of precision die cutting is evolving, shaped by advancements in technology and shifting market demands. Here are some emerging trends that are likely to define its future:
Technological Innovations Enhancing Die Cutting Precision
Technologies such as 3D printing and advanced software design tools are revolutionizing the die cutting landscape. These innovations enhance design capabilities, allowing for more intricate and complex parts to be produced with greater ease. Moreover, automation technology streamlines processes, increases efficiency, and reduces human errors.
The Role of Automation in Precision Die Cutting
As industries seek to increase production efficiency, automation in precision die cutting is becoming more prevalent. Automated systems allow for quick setup times, reduced labor costs, and consistent production output. This trend is particularly beneficial in high-volume manufacturing environments where precision and speed are critical.
Sustainability Practices in Die Cutting Operations
With increasing awareness of environmental impacts, sustainability is becoming more prominent in die cutting operations. Companies are exploring eco-friendly materials, reducing waste through improved cutting strategies, and implementing recycling programs. Embracing sustainability not only benefits the planet but also enhances a manufacturer’s marketability and aligns with consumer preferences.
Leave a Comment