Choosing the Right Nitrogen Regulator: A Comprehensive Guide for Professionals
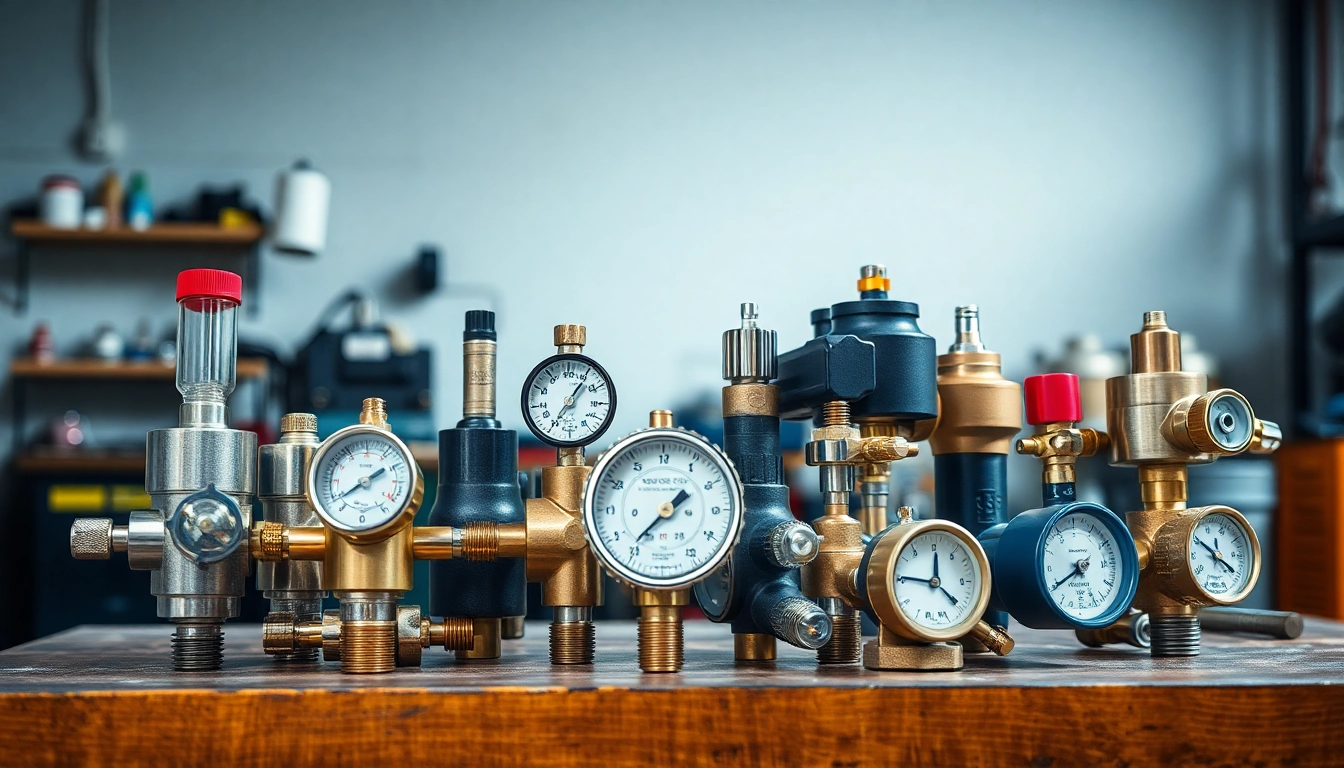
Understanding Nitrogen Regulators
Nitrogen regulators are critical components in many industrial and medical applications, ensuring the safe and efficient delivery of nitrogen gas from a high-pressure source to the desired pressure for use. By controlling the outlet pressure and allowing for effective flow regulation, these devices play a vital role in various operations. In this article, we will delve into the specifics of nitrogen regulators, exploring their types, applications, installation best practices, and safety considerations. If you’re in need of a nitrogen regulator, understanding these aspects will help you make an informed choice.
What is a Nitrogen Regulator?
A nitrogen regulator is a device used to control the pressure of nitrogen gas released from a storage tank or cylinder. It ensures that the nitrogen is delivered at a consistent, lower pressure suitable for various applications such as inflation, purging, and pressure testing. Regulating pressure is necessary to prevent damage to systems and equipment that may occur if exposed to excessive pressure levels.
The Importance of Pressure Regulation
Pressure regulation is crucial for maintaining safety and efficiency in operations. In industrial settings, high-pressure nitrogen may be used for applications such as food preservation and chemical processes. In medical contexts, precise control over the delivery pressure is essential for tools and equipment like anesthetic systems. An effective nitrogen regulator guarantees that the output pressure remains within safe operational limits, reducing the risk of accidents and equipment failure.
Applications of Nitrogen Regulators
Nitrogen regulators are utilized across a wide range of industries, including:
- Food and Beverage: Used for pressurizing beer kegs and maintaining nitrogen levels in packaging to prolong freshness.
- HVAC and Refrigeration: Crucial in pressure testing HVAC systems and purging lines.
- Aerospace and Automotive: Employed in structural testing and fuel systems where low-pressure gas is required.
- Medical: Essential in the proper functioning of surgical tools that require precise nitrogen pressure for operation.
Types of Nitrogen Regulators
Fixed vs. Adjustable Nitrogen Regulators
Nitrogen regulators can be categorized into two primary types: fixed and adjustable regulators. Fixed regulators deliver nitrogen at a preset pressure, making them ideal for applications that require consistent pressure levels without variation. On the other hand, adjustable regulators allow users to vary the outlet pressure, providing flexibility for operations that demand different pressure settings. Choosing the appropriate type depends on the specific operational needs of the application in question.
Single vs. Dual Outlet Options
Another important consideration is whether to opt for a single or dual outlet nitrogen regulator. Single outlet regulators are sufficient for straightforward applications where only one output stream is needed. In contrast, dual outlet regulators are beneficial in complex operations where multiple systems require nitrogen simultaneously. This allows for more streamlined operations without the need for additional equipment.
Specialized Nitrogen Regulators for Industries
Many industries have specific requirements for nitrogen delivery that necessitate specialized regulators. For example, regulators designed for welding applications have features tailored to handle higher flow rates and pressures. Similarly, medical-grade nitrogen regulators must meet stringent regulatory standards to ensure patient safety. Understanding the unique requirements of your industry will help in selecting the right nitrogen regulator for your needs.
Choosing the Right Size and Capacity
Determining Flow Rate Requirements
Correctly sizing a nitrogen regulator involves assessing the flow rate requirements of your application. Flow rate is typically measured in standard cubic feet per hour (SCFH) or liters per minute (LPM). Understanding the demands of your specific application, whether it is a quick release for a pneumatic tool or a steady supply for food preservation, will guide you in choosing a regulator with an adequate flow capacity.
Understanding Pressure Ratings
Every nitrogen regulator comes with a specified pressure rating detailing its maximum outlet pressure. It is critical to ensure that the regulator’s rating aligns with the demands of your application. Using a regulator outside its rated capacity can lead to failure or unsafe conditions. Confirming compatibility with your nitrogen source is an essential step in the selection process.
Compatibility with Existing Systems
Ensuring compatibility with existing systems is vital when selecting a nitrogen regulator. Check for inlet connections, thread types, and whether the materials used can handle the nitrogen environment. Incompatibilities can lead to leaks or system failures, emphasizing the importance of a thorough review of operational needs.
Installation and Maintenance Tips
Proper Installation Techniques
Installing a nitrogen regulator requires precision and attention to detail. Follow these general guidelines for proper installation:
- Ensure that all components are clean and free of contaminants.
- Use appropriate tools to avoid damaging fittings and connections.
- Securely fasten the regulator to the nitrogen source, ensuring there are no gaps or leaks.
- Conduct a thorough leak test after installation to ensure system integrity.
Routine Maintenance Best Practices
Regular maintenance is essential for the long-term performance of nitrogen regulators. Here are best practices:
- Inspect for leaks regularly, especially at fittings and connections.
- Clean or replace filters as recommended by the manufacturer.
- Check pressure gauges for accuracy and replace if malfunctioning.
- Monitor performance during operation for any fluctuations that may indicate wear.
Signs of Wear and When to Replace
Understanding when to replace a nitrogen regulator is critical to maintaining system safety and efficiency. Signs that a regulator may need replacement include:
- Unstable pressure readings.
- Difficulty adjusting pressure settings.
- Visible signs of corrosion, wear, or damage.
- Increased frequency of leaks despite sealing efforts.
Safety Considerations with Nitrogen Regulators
Working Safely with Gases
Safety is paramount when working with gases like nitrogen. While nitrogen is inert and non-toxic, it can displace oxygen in confined spaces, leading to suffocation hazards. Always ensure adequate ventilation and use nitrogen regulators in well-ventilated areas. Furthermore, following proper handling procedures minimizes the risk of accidents during operation.
Emergency Procedures and Protocols
Establishing emergency procedures for incidents involving nitrogen regulators is essential. Ensure staff members are trained in recognizing signs of potential hazards and responding appropriately. Develop clear protocols for evacuating areas in the event of a nitrogen leak or other emergencies. Regular drills and training help reinforce safety practices.
Regulatory Compliance in Handling Nitrogen
Compliance with local and national regulations regarding gas handling is essential for safety and legal practices. Familiarize yourself with the guidelines that apply to your operations and ensure all personnel handling nitrogen regulators adhere to these standards. This includes proper storage, transportation, and operation of nitrogen equipment.
Leave a Comment